An In-Depth Look at the Core Components of a Hydraulic System
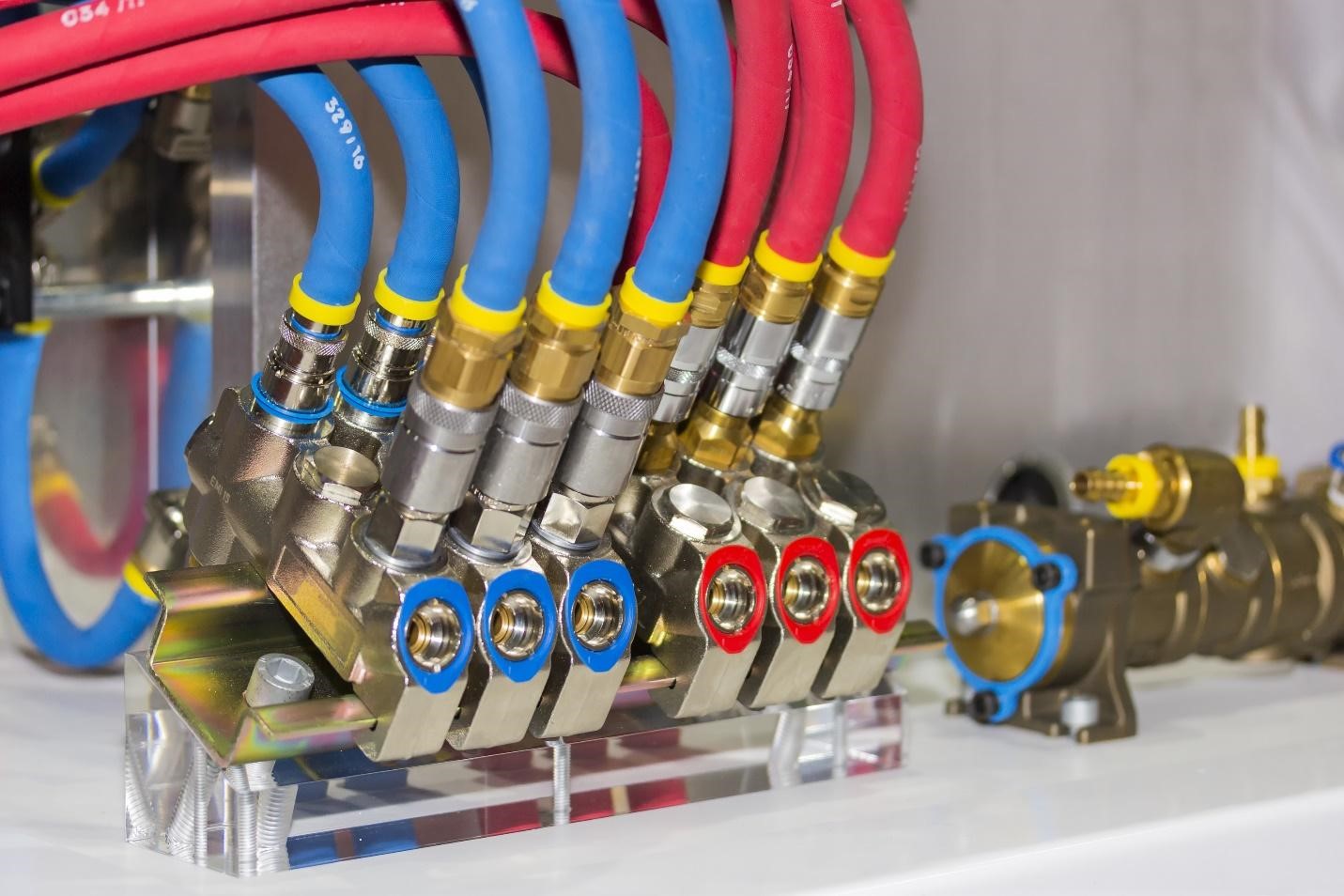
In the world of modern engineering, hydraulic systems stand as intricate assemblies of several sophisticated machinery components working in unison to fulfill a designated objective. Predominantly, these objectives revolve around motion, such as moving a piston or transferring fluids across the system. This comprehensive guide aims to delve deeper into the primary elements that compose a hydraulic system and provide a brief overview of their functionalities.
The Lifeline of the System: Hydraulic Hoses
These sturdy conduits form the lifelines of a hydraulic system, serving as the primary channels for fluid transportation. Hydraulic hoses connect to various system components, including pumps, valves, hydraulic cylinders, and others. These hoses exhibit significantly superior durability than an ordinary garden hose. This characteristic is crucial as they handle the conveyance of more aggressive fluids, such as oil, enabling the hydraulic system to function efficiently.
When installing these durable conduits, one needs to be mindful of their minimum bend radius. This term represents the smallest permissible radius to which you can bend the hose without inflicting damage to the inner tube or the reinforcement layer. As fluids inherently follow the path of least resistance, they exert pressure on the hose’s internal seals in an attempt to find an escape route. By exceeding the bend limit and jeopardizing the inner tube and reinforcement layer’s structural integrity, the pressurized fluid may potentially cause leaks or bursts at the bend.
The Essential Medium: Hydraulic Fluids
A hydraulic system is incomplete and non-functional without the presence of a fluid medium. While water can serve as a hydraulic fluid, several factors make it less than ideal. The boiling point and freezing point of water can lead to operational failures in extreme weather conditions, and its tendency to corrode metal reduces the system’s overall lifespan.
However, there are specific situations where water could function effectively as a hydraulic fluid. But for most hydraulic systems, oils are the preferred choice due to their wider temperature tolerance range and their ability to lubricate metal components instead of corroding them.
The Storage Hub: Reservoir Tank
The reservoir tank’s principal role is to store fluids for the pump’s consumption, but it also performs a multitude of additional functions. It compensates for hydraulic fluid losses over time by carrying an excess amount, allowing the system to run without requiring frequent refilling. Besides, it aids in cooling down the fluids and partially purifying them of contaminants.
The Energy Converter: Hydraulic Pump
Hydraulic pumps play a critical role in transporting hydraulic oil to its intended destination. They transform mechanical energy into hydraulic energy to fulfill the system’s objectives. In a more specific sense, hydraulic energy comprises the pressurized force exerted by the compacted fluid and the flow power given by the pump’s propulsion.
The Powerhouse: Actuator
Actuators, or hydraulic cylinders, are responsible for reverting hydraulic energy back into mechanical energy. Using the physical force of the pressurized hydraulic liquid, actuators manage to move mechanically. For instance, in a dump truck, hydraulic fluids powered by the pump provide the actuators with the energy required to extend mechanically and unload the truck’s payload.
Actuators can be classified into three main types:
- Linear Actuators: These actuators execute motion only in a straight line, such as up and down or left and right.
- Rotary Actuators: Unlike linear actuators, rotary actuators perform full 360-degree rotations.
- Semi-Rotary Actuators: These actuators operate similarly to rotary actuators, but they do not complete full rotations. Instead, they rapidly turn in one direction before switching to the opposite direction.
The Flow Controllers: Valves
Everyone encounters valves in their daily life, like when washing hands in a bathroom. In a hydraulic system, valves control the fluid’s direction. They come in different varieties, each serving a unique role:
- Pressure Control Valve: This valve type incorporates a pressure transmitter that senses the fluid’s pressure intensity. It communicates this information to the valve electronically, dictating when the valve should close or open.
- Flow Control Valve: Similar to the pressure control valve, the flow control valve uses a flow transmitter that measures the fluid’s flow rate and informs the valve when to initiate or cease fluid flow.
- Directional Control Valve: This unique valve type allows system operators to control the fluid’s trajectory. It helps guide the fluid in the desired direction instead of letting it follow the path of least resistance determined by the pump’s push.
The Guardians of the System: Filters
Although the reservoir may provide some level of purification, filters act as the primary defense against system contamination. They capture and remove most of the dirt and impurities present in the oil, protecting the system from potential harm.
The Heart of the System: Power Source
The power source, the linchpin of the hydraulic system, is typically a hydraulic motor. You pour oil into it, switch it on, and it powers the system like any other engine. However, you have an alternative in the form of a hydraulic power pack or a hydraulic power unit. This all-in-one unit combines a motor, fluid reservoir, and pump.
When you think of hydraulic and industrial hose services, PIRTEK Canada stands as an industry leader. Our highly skilled experts deal with hydraulic hose-related problems daily, providing superior solutions. If you are facing difficulties with your hydraulic hoses, get in touch with your local PIRTEK Canada location, or visit our website for further details.
MEDIA INQUIRES
For media inquiries, please contact:
PIRTEK Canada Brand Marketing, marketing@pirtekcanada.ca