Strategies for the Optimal Upkeep of Hydraulic and Industrial Hoses in 2023
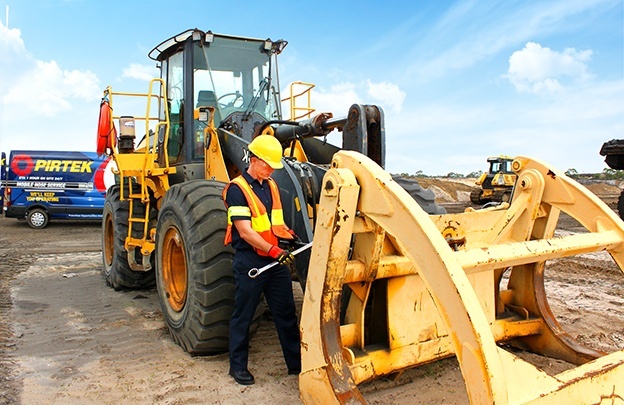
Hydraulic and industrial hoses are pivotal components in a multitude of businesses, with their operational integrity directly affecting profitability and safety. A hose failure, besides disrupting production, may lead to significant environmental cleanup costs and potentially damage a company’s credibility. Moreover, a ruptured hose under high pressure or a brittle hose with an inadequate fitting can pose a significant risk to personnel, causing injuries or leading to accidents. Thus, proactive maintenance of these crucial components should be a top priority.
Here are five key strategies for effective hose maintenance:
1. Regular Inspection of Hoses and Fittings
Regular inspections can go a long way in preventing hose failures. A general rule is to inspect your hydraulic hoses and fittings every 600 operating hours or every three months, although these intervals may need adjusting depending on the specific circumstances. For instance, if your hoses are operating under high impulse cycles, extreme temperatures, high pressures, or in challenging environments, they may require more frequent inspections.
A thorough inspection should include a complete lockout/tagout procedure to ensure the safety of the person conducting the inspection. Look for visible signs of wear and tear such as cracks, splits, missing covers, exposed reinforcements, abrasions, blisters, and broken clamps. The positioning of the hoses is crucial, too, as they must have enough slack to accommodate movement during use without causing kinks or twists.
In addition to scheduled inspections, operators should maintain a constant awareness of hose safety. Daily checks can reveal early signs of issues like fluid leaks, frayed hoses, or dampness behind the ferrule. Any unusual behavior in the machinery, such as unusual sounds or sluggish response, should also prompt and immediate inspection.
2. Maintenance Logs and Hose Tagging
Record-keeping plays a pivotal role in proactive hose care. Detailed logs of inspection results, repairs, and hose replacements can help you track the ‘health’ of each hose and its fittings, identify older hoses requiring more attention, and predict potential failures.
One effective way to streamline the inspection process is through hose tagging, a system that assigns a unique identifier (such as a barcode) to each hose. This identifier can be linked to the hose assembly’s Bill of Materials, manufacturing information, test reports, and other relevant data, enabling accurate tracking of hose performance and life cycle.
This approach aids in predicting when a hose might reach the end of its operational life based on factors like productivity, operating hours, workload, and impulse cycles.
3. Thoughtful Selection of Hoses and Fittings
Choosing the right hydraulic or industrial hose and fittings requires careful consideration of various factors. These include the type of substance the hose will convey, the volume of fluid or gas it will handle, the pressure, velocity, and temperature requirements of your system, and the specific work environment.
Different substances interact differently with hose materials, which is why hydraulic hoses have a chemical compatibility rating. Similarly, the hose size should correspond to the capacity of your hydraulic system.
The application of the hose also dictates the choice of hose and fittings. For instance, hoses for heavy machinery like earthmovers or excavators operating in harsh environments may require additional protection such as textile, metal, or plastic sleeves. Less aggressive environments like power steering systems or lubrication systems require different types of hoses.
It’s also crucial to ensure that your hoses and fittings are compatible. Even if they’re not from the same manufacturer, they should work well together – something you can verify with the manufacturers.
4. Proper Installation of Hoses and Fittings
Once you have the right hoses and fittings, the next critical step is proper installation. This involves accurate measurement of hose length (which should account for the necessary movement during operation), the right hose cutting tools, ensuring that the cut ends are clean and free from debris, and correct positioning to prevent exceeding the hose’s bend radius.
When installing new hoses, ensure they are assembled in a clean environment to prevent contamination. All components should be visually inspected before assembly. When cutting the hose, use tools that match the hose type to avoid causing damage that may lead to premature failure. Ensure that the fittings are tightened to the manufacturer’s specifications.
5. Preventing System Contamination
Hydraulic systems are highly susceptible to contamination from tiny debris pieces, either during filling with oil or other fluids or over time as the components wear and corrode.
Regular oil sampling can help you monitor the system’s cleanliness by tracking the particle count and identifying issues early on. You should also use filtration systems where appropriate to remove contaminants.
In specific environments or applications, adding an extra inline filter within the hydraulic system might be beneficial, providing another layer of protection against system contamination. It’s crucial, however, to maintain and replace these filters regularly to keep them effective.
Conclusion
While investing time and resources in preventive hose maintenance might seem daunting, it’s a strategy that pays off. With a well-implemented maintenance program, such as the one offered by PIRTEK Canada Service & Supply Centers, you can minimize equipment downtime, prevent worker injuries, avert environmental hazards, and save on wage losses. The benefits extend beyond these, though, as a reliable, well-maintained system contributes to a company’s credibility, boosting its reputation for dependability and high-quality standards.
MEDIA INQUIRES
For media inquiries, please contact:
PIRTEK Canada Brand Marketing, marketing@pirtekcanada.ca